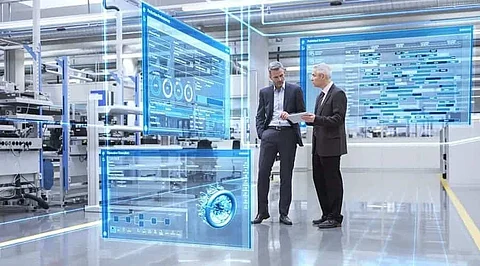
proposes that, by 2020, worldwide manufacturers will put $70 billion in IoT solutions and numerous manufacturers are deploying IoT devices to use prescient predictive maintenance and advanced data analytics to improve profitability, accessibility and enhance their business contributions.
With the number of smart devices set to arrive at 31 billion by 2020 and increment to 75 billion by 2025, it's basic that organizations comprehend the manner in which these gadgets are changing conventional methods of working into dynamic, interconnected systems. Through the use of IoT, challenges in manufacturing and all through the supply chain can be limited by IoT sensors.
Manufacturers and industrialists in each area have a critical opportunity nearby where they can screen as well as automate huge numbers of complex processes engaged with manufacturing. While there have been systems which can track progress in the plant yet the industrial IoT (IIoT) technology gives unmistakably more intricate details to the managers.
Flaws and inadequacy in the final product upsurge expenditure and overburden workers in an assembling cycle. To alleviate these issues, producers can use the IIoT features and one such is Digital Twins. It imitates the developing product in a digital form. By retrofitting sensors, manufacturers assemble information about their gear's whole working system and the expected yield from every unit. The data, ingested from the digital replica, empowers decision-makers to examine the efficiency, effectiveness, and accuracy of the system. It likewise helps in distinguishing possible bottlenecks in their product that encourages directors to make a better version of the products.
Through interfacing IoT-driven gadgets that have distinctive sensor points (temperatures, vibration, voltages, flows, and so on) to different gadgets, IFTTT, cloud/API or legacy systems manufacturers can acquire fundamental maintenance information. This sort of data permits to gauge the current state of hardware, decide warning signs, transmit alerts and activate corresponding repair processes.
This way IoT changes maintenance into a relentless and automated practice, which anticipates failure a long time in advance. Besides, it encourages cost savings over traditional preventive measures as the moves are made precisely when they are fundamental.
Getting legitimate information in time, managers can detect plant machinery that requires fixing. Plus, it assists with arranging upkeep activities altogether and holds systems online as workers are still performing the task. IoT may prolong equipment lifetime, add to plant safety and lower the dangers of mishaps that affect the environment adversely.
The utilization of IoT sensors in manufacturing equipment empowers condition-based maintenance alerts. There are numerous basic machine tools that are intended to work within a certain temperature and vibration ranges. IoT sensors can effectively screen machines and send a notification when the hardware strays from its endorsed parameters. By guaranteeing the endorsed working climate for machinery, manufacturers can preserve energy, eliminate machine downtime and increase operational efficiency.
IoT devices track and follow the inventory state in real-time. Producers can screen their supply chain by having real-time insights into the accessible assets. It incorporates data identified with the Work in Process, hardware collection, and the delivery date of required raw materials. Some of the IoT providers additionally give the integration of their IoT solutions with the current ERP frameworks of manufacturers which wipes out the requirement for manual documentation for operations. It provides the facility of cross-channel visibility into various departments and enables the partners in inspecting the undergoing progress, which consequently lessens the expenditure because of mismanagement and lack of analysis in the company.
Increasingly manufacturing ventures will in general execute asset practices. IoT innovation joined with the advancement of native web and mobile apps for iOS or Android makes it conceivable to acquire real-time asset information and make reasonable decisions.
The significant task of following lies in discovering and overseeing such vital resources as the parts of the supply chain (raw materials, containers, and finished goods). Such applications can radically streamline logistics, keep uploads of work in progress, and reveal thefts and infringement. IoT-based asset tracking enables the manufacturers to compute the use of movable equipment elements and start measures to abbreviate idle period and enhance utilization.
IoT when combined big data analysis can improve the overall workers' safety and security in the plant. By checking the Key Performance Indicators (KPIs) of health and security, such as number of wounds and sickness rates, close misses, short- and long-term absences, vehicle incidents and property damage or loss during daily operations. In this manner, effective monitoring guarantees better security. Slacking pointers, assuming any, can be addressed to consequently guaranteeing appropriate redressal health, safety, and environment (HSE) issues.
IoT is consistently improving communication and advancing assembling processes, with more applications and solutions being grown continually. Microsoft as of late reported that it's uniting with the BMW Group to change digital production efficiency across the business with an IoT open manufacturing platform. With this present, obviously many are beginning to exploit this ground-breaking innovation and, therefore, are increasing profitability and proficiency, as well as gaining a more profound understanding into their customers' behavior patterns and needs.
Join our WhatsApp Channel to get the latest news, exclusives and videos on WhatsApp
_____________
Disclaimer: Analytics Insight does not provide financial advice or guidance. Also note that the cryptocurrencies mentioned/listed on the website could potentially be scams, i.e. designed to induce you to invest financial resources that may be lost forever and not be recoverable once investments are made. You are responsible for conducting your own research (DYOR) before making any investments. Read more here.