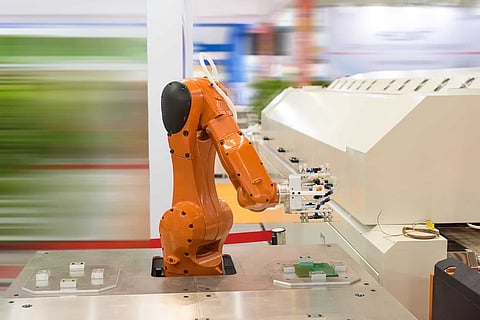
Robotics has ventured into a variety of industries to drive better efficiency. Specifically, in the manufacturing field, its advents are quite commendable. For example, for its assembly line, Henry Ford inherited stationary robotic units that are positioned "behind the fence" and away from humans. This allows the robots to do their work without harming workers. Such robots are extremely energetic and don't get fatigued. This is what personifies efficiency.
However, efficiency is not the sole advantage offered by robotics, manufacturers are also considering the implementation of the technology to planning and shop-floor operations. As noted by Andreas Bauer who is a Team Lead at University Datacenter (University of Augsburg), robotics can help some enterprises more flexibly program customizations into the assembly process – so this car gets a sunroof, and that one gets the sports trim. This flexibility allows manufacturers to accommodate customer preferences with greater ease.
As assembly lines are still common, the robotics implementation is shifting towards flexible machines as well. With its self-learning capabilities that help optimize processes over time, leveraging robotics at such a scale helps fuel a much higher degree of modularization in production.
However, it is necessary to acknowledge not all manufacturing requires the same robotics support. Possibly, an auto manufacturer follows different processes than a manufacturer of semiconductors. Therefore, for robots to be more broadly adopted, they need to be made in a domain-agnostic way.
Andreas says, robot functionality, in a sense, needs to be modularized which requires a certain amount of standardization across use cases. Basic equipment – such as motion sensors, grippers, joints, voice recognition systems, and welding cells – can be used across models and quickly adapted to a wide range of requirements and unique use cases.
In Horizons by SAP, he quotes that, "as robots are used as part of complex processes manufacturing and otherwise – this notion of standardization needs to extend to backend business and operational systems as well. One area ripe for progress is the technological integration of robots into MESs. By creating robotics that can flexibly adapt to specific use cases and still interoperate with other applications, companies could improve the networking and interdependency among these technologies."
Moreover, while progress in standardization is still needed, robots are already being employed to make personalization feasible in terms of cost, timely delivery, operational logistics, and other key metrics. Manufacturers can use robots to enhance customization, even with assembly-line production models. However, the production cell approach is leading the way forward in terms of increasing flexibility and responsiveness to customer demand.
Several companies in today's competitive era are competing in the arena of customer experience. In fact, the product created by manufacturers is an integral part of that experience. Amid this what can make a difference is that – the ability to personalize the product to unique customer expectations and requests.
Andreas says the production cell approach maximizes customization flexibility. With the collaboration of robots and humans, organizations can harmonize unique production runs. The result is sometimes called "mass customization" – or the ability to deliver what customers want with short lead times and optimal price points that drive both sales and profitability.
Moreover, consumer electronics companies can meet demands for storage capacity or screen size without producing large lots ahead of time and hoping to sell what's produced. Shoemakers, on the other hand, can open their design process to consumers and then deliver precisely what the customer has created.
Such mass customization is already happening today with robotics and modular production techniques. Furthermore, in the future, advancements in robotics will make it easier for manufacturers to bring their customers more intimately into the product experience – from design to production. Also, making the use of modular robotics technologies to increase personalization, manufacturers can increase customer engagement and increase loyalty over time.
Join our WhatsApp Channel to get the latest news, exclusives and videos on WhatsApp
_____________
Disclaimer: Analytics Insight does not provide financial advice or guidance. Also note that the cryptocurrencies mentioned/listed on the website could potentially be scams, i.e. designed to induce you to invest financial resources that may be lost forever and not be recoverable once investments are made. You are responsible for conducting your own research (DYOR) before making any investments. Read more here.