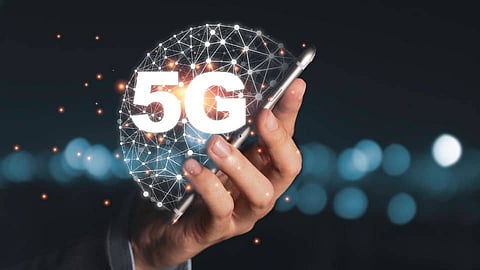
There has been a lot of talk about the new fifth generation of mobile networks (5G) and its role in the new industrial revolution. To call it a potential game changer is perhaps putting it lightly; the prospect of vastly superior bandwidth and speed over previous networks has major implications in all facets of society, not least of all in industrial manufacturing. As more infrastructure is installed, 5G will work with and in some cases replace existing fixed, wired connections, making an evolving manufacturing sector even more agile and prepared to take advantage of new innovations.
This article will explore some of the ways this is happening and how it is being implemented by different companies around the world.
Make no mistake, the mainstream use of Wi-Fi networks has been a transformative technology for small and large cap companies alike. In many countries however, mobile internet connections have proven themselves to be more reliable than Wi-Fi networks, a fact that has led some companies, particularly those in the automotive sector, to consider implementing their own private 5G network.
5G isn't simply a next-gen technology with slightly better specs; by all accounts 5G networks aim to provide speeds at least ten times greater than 4G networks and up to 50 times lower latency. Speed and latency aside, 5G networks have the ability to support many more connected devices than its predecessor, a selling point that does not go unnoticed by companies whose products and/or operations are heavily intertwined with the Internet of Things (IoT). Unlike 4G or wireless networks, 5G can be programmed to prioritize service to devices and components deemed critical to operations. In cases where service to the network is disrupted, the network can ensure mission-critical devices remain online.
Considering all of the above, is a private 5G network a worthwhile investment? German automaker Audi seems to think so. In the next few years, they plan on bringing their own 5G network online, and it's easy to see why. With an ever-increasing fleet of robots and other automation equipment in their warehouses and factories, it's important that their connection is reliable and that the transfer of data is as quick as possible. Audi is by far the only company, let alone automaker that is currently examining the cost-benefit analysis associated with implementing a private 5G network. It's likely that many of the world's largest manufacturers will follow suit in the years to come.
Other benefits of 5G include enhanced digitization of information and increased profitability (an estimate by the firm KPMG signals that 5G can add value to a couple equal to approximately 5% of their annual revenue).
The unparalleled speed of 5G might be the selling feature that most consumers will gravitate towards, but speed without a stable and reliable connection and low latency won't be much of an improvement. The combination of speed, enhanced bandwidth, low latency and reliability is allowing more manufacturers to leverage new and emerging technologies in ways they couldn't before. One such example is augmented reality, or AR.
One of the greatest impediments to profitability is equipment downtime especially when that downtime is due to an unexpected maintenance issue. AR can be used to help technicians to assess a piece of faulty equipment and troubleshoot the issue, getting the device back online in less time. Having the ability to overlay a digital layer and access detailed schematics of the piece of equipment rather than having to manually find the correct file is a much more efficient way for technicians to operate, as Ericsson, a multinational telecommunications giant came to understand. Prior to the adoption of AR technology, Ericsson's technicians spent approximately half of their work time performing tasks that added no value, such as locating all the necessary files and navigating troubleshooting instructions. The implementation of AR has meant that Ericsson's technicians have drastically reduced the amount of time spent trying to locate the issue and increased the amount of time that they perform activities that directly impact the profitability of the company.
Expediting repairs is one thing, but imagine having a network that can actually help to predict when a particular component or device may fail? Shoddy maintenance practices can take a big bite out of a manufacturer's financial health, reducing a plant's production capacity on average by 5-20%. What is a manufacturer to do? They could allow it to run until there is a problem or they could take the machine offline and give it a thorough inspection to ensure it will continue to run as expected. The problem with both of these approaches is the same: downtime, no matter the cause, halts production.
Though it is not practical to expect an asset to operate into perpetuity, there are ways to maximize the downtime that is planned while reducing the likelihood of unplanned downtime. Artificial intelligence and machine learning is already helping manufacturers to crunch vast amounts of data to try and anticipate when an asset will require maintenance, but the implementation of 5G technology will greatly increase the amount and speed at which this data is transferred for parsing.
Additive manufacturing, more commonly known as 3D printing, is not just for hobbyists. In fact, this technology is upending the way in which manufacturers obtain spare parts for machinery and other assets. The larger the manufacturer however, the more additive manufacturing they will do and the more printing devices they will need. Though 5G does not itself contribute to how spare parts are constructed on site, it does allow a remotely located operator to connect with and monitor numerous printing processes simultaneously.
Of course, a manufacturer could simply purchase and store spare parts on site, but that in and of itself represents several problems. The first, is the capital that needs to be tied up in spare parts. Parts are ordered and stored until they are needed so that repairs can be completed expeditiously. Some parts may have to be purchased in bulk and they may ultimately go unused. The second problem with buying and storing spare parts is the physical space that it consumes. Storing parts can overtake a significant portion of a factory's square footage resulting in a pretty significant opportunity cost; the more factory floor space that is devoted to storing parts, the less floor space can be devoted to producing goods and turning a profit.
Thanks to predictive analytics (resulting from the vast amounts of data collected over the 5G network) it is much easier to anticipate when a particular part will be needed and the company can schedule the production of the necessary component thanks to their on-site additive manufacturing capabilities.
These are just some of the ways that 5G is having a significant impact on what has become known as the Fourth Industrial Revolution, or Industry 4.0. Obviously, it's impact can be seen throughout smart factories and manufacturing facilities throughout the world and its influence will only continue to grow. If you're interested in learning more about obtaining an electronics technician certificate, be sure to check out what George Brown College has to offer.
Join our WhatsApp Channel to get the latest news, exclusives and videos on WhatsApp
_____________
Disclaimer: Analytics Insight does not provide financial advice or guidance. Also note that the cryptocurrencies mentioned/listed on the website could potentially be scams, i.e. designed to induce you to invest financial resources that may be lost forever and not be recoverable once investments are made. You are responsible for conducting your own research (DYOR) before making any investments. Read more here.