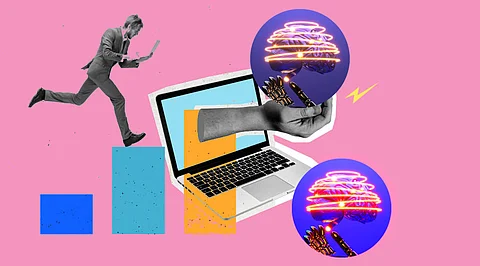
The explosion of advanced technology in the workplace may appear to be straight out of the novel Brave New World, but it contains genuine humanity. Workers' safety can be transformed from a business benefit to an employee benefit using artificial intelligence and data science tools.
Keeping employee populations safe reduces risk and workers' compensation insurance rates, increasing productivity, but it does so much more in a tight labor market and competitive business landscape. This is especially true in industrial settings where operating heavy machinery or lifting significant weight can be taxing.
In this article, we will see how AI and data science are changing job safety.
One of the most important lessons from the pandemic and Great Recession is the importance of creating a health and safety culture that demonstrates that employers care about their employees and will go to any length to retain top talent.
Using high-tech tools to improve workplace safety can lead to increased operational efficiency. Only 2% of the US$55 billion spent on workers' compensation in the United States is spent on safety, while up to 71% is spent on claims. Overexertion and bodily reaction issues are said to be the cause of nearly half of all injuries in industries where manual material handling is common.
However, there are numerous opportunities to reverse this trend, and benefits advisers can play an important role in guiding their clients down this path. We were able to identify 22 visually detectable causal risk factors that cause 90% of workplace injuries with the help of AI and data science. Ergonomics, being struck by equipment or objects, slip, trip, and fall incidents, being caught in various hazards, and product damage from accidents or mishaps are all major categories.
The problem with most safety programs is that they are reactive. Those in charge of an organization's work comp function and safety posture must usually wait for accidents to occur before they can address hazards. In short, they can't make changes until a pattern of injuries and accidents has been established.
The vast majority of these incidents are cumulative, and there are numerous examples of near misses and hazards that put people in danger daily. Having objective methods of measuring them and comprehending the potential impact will aid in prevention and raise the bar on worker safety. This includes using benchmarks to determine which facilities and zones need the most improvement, as well as updating operations scorecards with predictive safety key performance indicators.
Your employer clients are likely to already have the video cameras required for the scalable collection of objective data; internet connectivity and low-cost camera systems can collect all of this video data from the workplace.
All an organization needs to do is upload the video, which allows a company with the right AI technology to quickly process that data and generate objective metrics that compare various risk factors in that facility to facilities within the same organization or other companies with similar types of operations. This provides enough context for an employer to develop a predictive model that shares the likelihood of an accident based on the hazards and frequency of hazards seen inside facilities.
AI has advanced to the point where two-dimensional video can generate thousands of data points that reveal when forklifts endanger the lives of anonymized individuals, or more subtle safety risks from repetitive activities, such as how long it takes between cycles of stress on the body. AI can recommend strategies to reduce stress, even if it is as simple as using a tool to improve one's reach and avoid a hunched position.
The lower and upper back, as well as the neck and shoulder, are some of the most common and costly injuries that develop over time. Back injuries are frequently chronic and can last a lifetime, which is why it's critical to address potential causes as soon as possible before they escalate into a US$1 million claim.
However, preventing these tragedies benefits more than just employees. There is also an advantage for businesses. The indirect costs of injuries, which can be two to five times the direct costs, are frequently overlooked. Administrative overhead and lost production time involving employees with critical knowledge or skills, as well as recruiting and training costs, may be included.
Join our WhatsApp Channel to get the latest news, exclusives and videos on WhatsApp
_____________
Disclaimer: Analytics Insight does not provide financial advice or guidance. Also note that the cryptocurrencies mentioned/listed on the website could potentially be scams, i.e. designed to induce you to invest financial resources that may be lost forever and not be recoverable once investments are made. You are responsible for conducting your own research (DYOR) before making any investments. Read more here.